The Ultimate Guide to Plastic Injection Molding Manufacturing
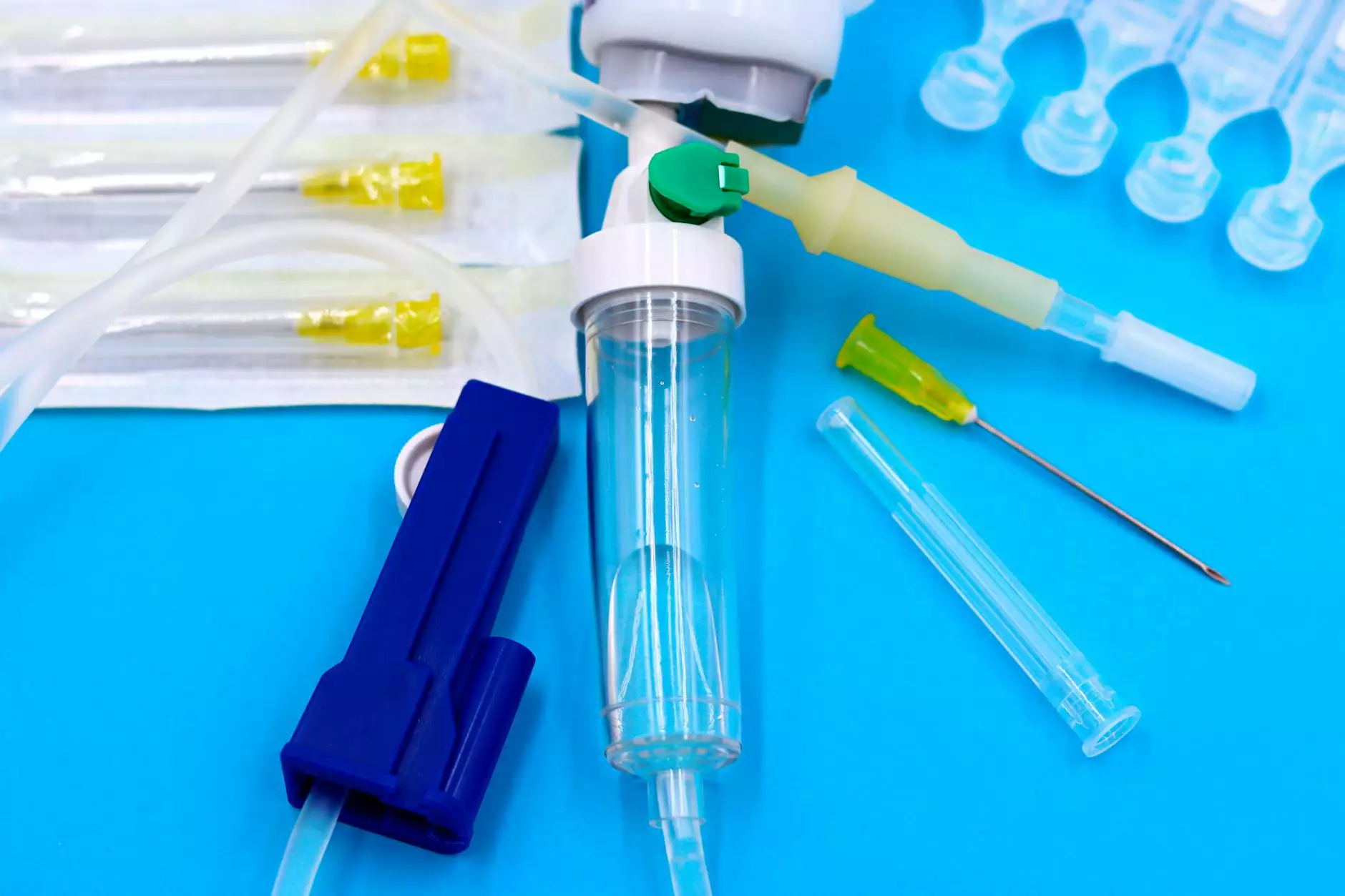
Plastic injection molding manufacturing is a transformative method that has become a cornerstone of modern industry. As the demand for precision and efficiency rises, this incredible technology continues to play a pivotal role in shaping the products we use daily. In this comprehensive guide, we will explore every aspect of plastic injection molding manufacturing, why it is essential for businesses, and how companies like Sumiparts can help you leverage its benefits.
Understanding Plastic Injection Molding
Plastic injection molding is a process that involves injecting molten plastic material into a mold to create a desired shape. This process is widely recognized for its efficiency, speed, and capability to produce high volumes of identical parts.
The Process of Plastic Injection Molding
The plastic injection molding manufacturing process consists of several stages:
- Designing the Mold: The initial step involves creating a detailed design of the mold. This design must take into account the product's specifications and the material characteristics.
- Preparing the Materials: The next step is selecting the right plastic polymer, which will be heated until it becomes molten.
- Injection: The molten plastic is injected into the mold under high pressure, ensuring that it fills every cavity completely.
- Cooling: After injection, the material is allowed to cool and solidify within the mold.
- Mold Removal: Once the plastic has solidified, the mold is opened, and the finished part is ejected.
- Finishing Touches: Depending on the specifications, additional processes like trimming, painting, or assembling may take place.
Advantages of Plastic Injection Molding
Plastic injection molding manufacturing offers numerous advantages that make it a preferred choice for many businesses:
- Efficiency: The process can produce high volumes of products quickly, which is crucial for meeting consumer demands.
- Cost-Effectiveness: Although the initial setup costs can be high, the per-unit costs decrease with larger production runs.
- Design Flexibility: The technology allows for complex shapes and intricate designs that would be impossible or costly with other manufacturing methods.
- Material Variety: A wide range of plastic materials can be used, enabling tailored solutions to specific industry needs.
- Durability: Parts manufactured using this technique are known for their strength and resilience, making them suitable for various applications.
Applications of Plastic Injection Molding
Plastic injection molding is employed across multiple industries, showcasing its versatility. Common applications include:
- Automotive Components: Parts such as dashboards, bumpers, and interior fittings.
- Consumer Goods: Products ranging from toys to household items.
- Electronics: Enclosures and components for various electronic devices.
- Medical Devices: Precision parts that demand high standards for safety and functionality.
- Aerospace: Lightweight parts that contribute to the performance and efficiency of aircraft.
The Role of Sumiparts in Plastic Injection Molding Manufacturing
At Sumiparts, we understand the complexities involved in plastic injection molding manufacturing. Our commitment to quality and precision makes us a reliable partner for businesses seeking to optimize their production processes.
Machining Excellence
Our machining services complement our molding capabilities, allowing us to provide fully finished parts that meet your exact specifications. We utilize advanced machinery and skilled technicians to ensure maximum accuracy and efficiency.
Laser Cutting for Precision
We also offer laser cutting services that enhance the precision of components used in injection molding. This technology allows for intricate cuts and shapes that enhance product design.
Welding for Strong Bonds
Our welding services further strengthen the products we manufacture, ensuring that all assembled components are secure and durable. This is particularly important in industries like automotive and aerospace, where the integrity of each part is critical.
Vulcanization for Enhanced Durability
In addition, we provide vulcanization services to improve the resilience of rubber components. This is beneficial for products that require flexibility alongside strength.
Choosing the Right Partner for Plastic Injection Molding
Selecting the right partner for plastic injection molding is crucial for the success of your manufacturing processes. Here are some tips to consider:
- Experience: Look for a company with a proven track record in the industry and expertise in multiple manufacturing processes.
- Technology: Ensure they utilize advanced technology and machinery to enhance efficiency and precision.
- Client Testimonials: Check for reviews or case studies that reflect their capability to deliver results.
- Custom Solutions: A good partner should be able to provide tailored solutions to meet your specific needs.
Future Trends in Plastic Injection Molding Manufacturing
The future of plastic injection molding manufacturing looks promising, with several trends expected to shape the industry:
- Automation: The incorporation of automation and robotics will lead to increased efficiency and reduced labor costs.
- Biodegradable Materials: Sustainable practices will become more prevalent, with a growing emphasis on using eco-friendly materials.
- 3D Printing Integration: Combining traditional molding with 3D printing will allow for more complex designs and prototyping.
- Smart Manufacturing: The use of IoT and data analytics will enhance production efficiency and quality control.
Conclusion
In conclusion, plastic injection molding manufacturing is an indispensable process that drives innovation and efficiency in numerous industries. Understanding its nuances and staying ahead of trends can position your business for success. Partnering with a skilled provider like Sumiparts ensures that you receive the highest quality products and services. Embrace the power of plastic injection molding and explore the endless possibilities it offers.
If you’re interested in learning more or are looking for a reliable partner in plastic injection molding manufacturing, contact us today!