Maximizing Efficiency with Downhole Filters in the Construction Industry
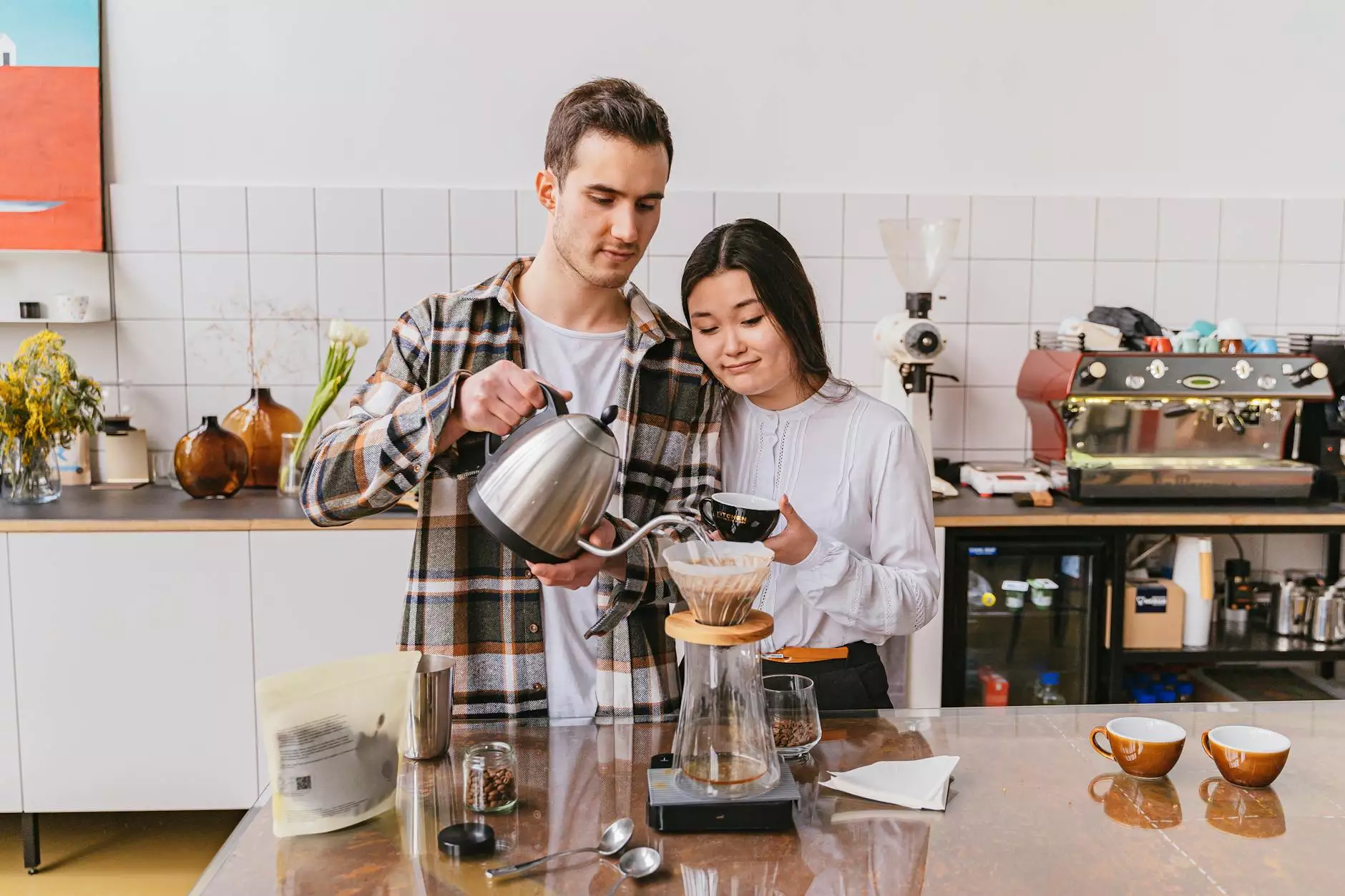
In today's competitive business landscape, efficiency and precision are paramount, especially in the construction sector. Companies like Maverick Drilling have recognized the importance of utilizing advanced technologies and equipment to optimize their operations. One crucial component making waves in this industry is downhole filters.
Understanding Downhole Filters
Downhole filters are specialized devices used to filter out unwanted materials from drilling fluids in various drilling applications. They serve a critical role in maintaining the integrity of the drilling process by preventing debris from entering the wellbore, which can lead to complications and increased costs.
The Importance of Downhole Filters
The integration of downhole filters in the drilling operation has several advantages that contribute to enhanced performance and reduced operational risks. Some of the key reasons businesses in the construction industry should consider incorporating these filters include:
- Improved Equipment Longevity: By preventing contaminants from damaging drilling equipment, downhole filters help prolong their lifespan and ensure they operate at peak efficiency.
- Cost Efficiency: Reducing downtime due to clogged equipment or operational failures translates into significant cost savings for drilling projects.
- Enhanced Safety: Effective filtration can mitigate risks associated with drilling accidents, ensuring a safer working environment for all personnel involved.
- Operational Efficiency: Streamlined processes lead to faster project completion times and improved overall productivity.
Applications of Downhole Filters in Construction
Downhole filters are versatile and can be applied in various scenarios within the construction industry. Here are some specific applications:
1. Oil and Gas Drilling
In oil and gas drilling, downhole filters play a vital role in separating solids from liquids. This helps in maintaining the viscosity of the drilling fluid and prevents the formation of harmful clogs, which can significantly delay the drilling process.
2. Geothermal Energy Extraction
During the geothermal drilling process, downhole filters ensure that the extraction fluids remain uncontaminated. This is crucial for maintaining efficiency and protecting sensitive drilling equipment.
3. Water Well Drilling
In water well applications, downhole filters are essential for preventing sand and silt from entering the well, which can lead to premature pump failure and costly repairs.
4. Mining Operations
Mining operations often involve drilling through contaminated land. Downhole filters help in filtering out harmful substances, thus enhancing the quality of the extracted materials and ensuring the safety of workers.
Types of Downhole Filters
Understanding the various types of downhole filters on the market is essential for selecting the right one for your operations. Here are some common types:
1. Wire Mesh Filters
Wire mesh filters are designed to allow fluids to pass through while trapping larger particles. They are ideal for applications requiring high flow rates and are easy to clean and maintain.
2. Porous Ceramic Filters
These filters utilize ceramic materials to provide excellent filtration capabilities. They are best suited for applications involving corrosive fluids due to their chemical resistance.
3. Sintered Metal Filters
Sintered metal filters can withstand high temperatures and are often used in harsh environments. Their durability makes them suitable for demanding drilling applications.
Choosing the Right Downhole Filter for Your Project
When selecting a downhole filter, consider the following factors:
- Fluid Characteristics: Understand the nature of the drilling fluid and the contaminants that need to be filtered.
- Flow Rate: Choose a filter that can handle the required flow rates to maintain operational efficiency.
- Operating Environment: Consider the temperature and pressure conditions of the drilling environment to select a suitable filter material.
- Maintenance Needs: Look for filters that offer easy maintenance and cleaning to minimize downtime.
Maximizing Performance with Downhole Filters
Incorporating downhole filters into your drilling operations can significantly improve overall project performance. Here are a few strategies to maximize their effectiveness:
- Regular Inspection: Schedule routine inspections of filters to ensure they are functioning correctly and to clean or replace them as required.
- Monitor Performance: Keep track of the efficiency and effectiveness of filters by monitoring fluid clarity and flow rates.
- Training Personnel: Invest in training your team on the importance of downhole filtration and best practices for maintenance.
- Leverage Technology: Use advanced monitoring systems to track filter performance in real-time and make data-driven decisions.
The Future of Downhole Filtration Technology
The future of downhole filters looks promising, with ongoing advancements in materials science and engineering. Innovations in filtration technology are expected to lead to:
- Smart Filters: Filters that can self-monitor and report on performance, helping companies optimize operations.
- Advanced Materials: The development of new filter materials that offer enhanced durability and filtration capabilities under extreme conditions.
- Eco-Friendly Solutions: Focus on sustainable filtration solutions that minimize environmental impact while ensuring operational efficiency.
Conclusion
In conclusion, downhole filters are indispensable tools in the construction industry, particularly in drilling operations. They provide a multitude of benefits, from improved equipment longevity to enhanced safety and operational efficiency.
Companies like Maverick Drilling that leverage these technologies can gain a competitive edge in the marketplace. By understanding the various types of filters available and their applications, businesses can make informed decisions that lead to more efficient and successful drilling operations.
Ultimately, investing in high-quality downhole filtration systems is not just a choice; it’s a strategic move toward sustainable and efficient business practices in the ever-evolving construction landscape.