Revolutionizing Creative Industries with Cutting-Edge Business Strategies in Art Supplies, Product Design, and 3D Printing Using Forming Mould Technology
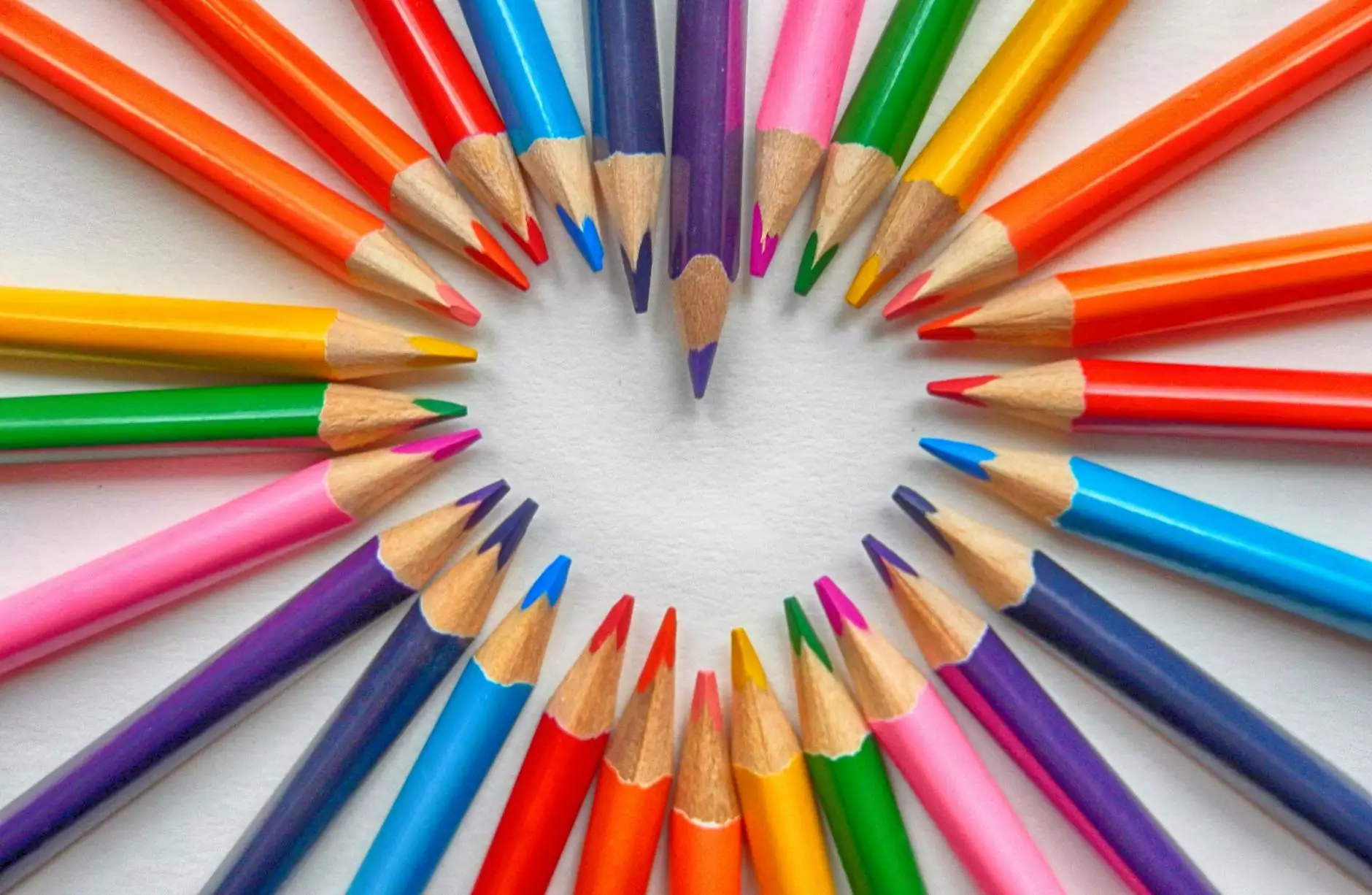
The landscape of modern business in the creative sector is undergoing a profound transformation, driven by innovative manufacturing techniques like forming mould. Companies like arti90.com are at the forefront, harnessing this technology to elevate their offerings in art supplies, product design, and 3D printing. This comprehensive guide aims to explore the multifaceted roles of forming mould in shaping competitive advantages, streamlining production, and fostering creative innovation within these dynamic industries.
Understanding the Power of Forming Mould in Business Innovation
At the core of manufacturing advancements lies forming mould technology—a process that involves shaping materials into predetermined forms through molds. Whether working with plastics, metals, or composites, the precision and efficiency of forming mould enable businesses to produce complex, high-quality products at scale. In art supplies, product design, and 3D printing, this technique unlocks new creative possibilities and reduces time-to-market, offering a competitive edge in a crowded marketplace.
The Basics of Forming Mould: From Concept to Reality
Understanding the forming mould process involves recognizing the different techniques such as injection moulding, blow moulding, compression moulding, and thermoforming. Each method caters to specific materials and product designs, allowing manufacturers to customize their approach for optimal results. The primary advantage of employing forming mould procedures lies in their ability to replicate intricate geometries with exceptional consistency and surface finish, vital for premium art supplies and innovative product prototypes.
Harnessing Forming Mould for Art Supplies Manufacturing
Elevating Art Material Quality Through Precision Moulding
The art supplies industry demands products that combine functionality, durability, and aesthetics. Forming mould techniques support the production of high-grade materials such as molded clay tools, brushes with ergonomic handles, and unique decorative mediums. By utilizing advanced moulds, arti90.com ensures the consistent quality of these products, minimizing defects while supporting large-volume production with minimal waste.
Customization and Unique Artistic Effects
- Personalized Art Supplies: Custom-shaped frames, palette knives, or brushes tailored to specific artists' needs
- Decorative Components: Intricate textured surfaces or embossed patterns achieved through detailed mould designs
- Sustainable Materials: Moulding biodegradable or recycled materials to meet eco-conscious demands
Impacts of Forming Mould on Innovative Product Design
Streamlining the Product Development Lifecycle
In product design, time and cost efficiency are paramount. Forming moulds allow designers to prototype rapidly and iterate designs without significant delays or expenses. This process supports rapid concept validation, enabling companies like arti90.com to bring creative ideas from sketches to market-ready products swiftly.
Enabling Complex Geometries and Aesthetic Excellence
Modern forming mould techniques facilitate the production of components with intricate curves, undercuts, and surface textures that traditional manufacturing methods struggle to achieve. For instance, innovative consumer electronics or luxury packaging benefits immensely from these capabilities, enhancing both functionality and visual appeal.
Design for Manufacturability (DfM) in Practice
Integrating forming moulds early in the design process ensures that products are not only creative but also cost-effective and easy to produce. This synergy results in less material wastage, simplified assembly, and shorter lead times—key factors that contribute to commercial success in competitive markets.
Transforming 3D Printing with Advanced Forming Mould Techniques
Synergizing 3D Printing and Moulding for Hybrid Manufacturing
While 3D printing offers unmatched freedom for rapid prototyping and small-batch production, integrating this with forming mould techniques enables scalability and mass production. Companies like arti90.com are pioneering this hybrid approach, where 3D printed prototypes inform the creation of durable, reusable moulds for volume manufacturing, dramatically reducing costs and lead times.
Enhancing 3D Printing with Custom Moulds
Customized moulds tailored for specific 3D printing applications facilitate high-precision casting and shrinkage control, ensuring every component meets exact specifications. This synergy opens new avenues for designing complex geometries, lightweight structures, and multi-material assemblies, vital for advanced art supplies and innovative consumer products.
Innovative Use of Forming Mould in 3D Printed Mass Production
- Speeding Up Production Cycles: Moulding reduces the bottleneck of layer-by-layer printing in mass production
- Cost Efficiency: Reusable moulds lower per-unit costs significantly over traditional 3D printing alone
- Quality Consistency: Moulded parts exhibit uniformity and impeccable surface finish
Why arti90.com Leads in Forming Mould Innovation
arti90.com combines deep expertise in forming mould technology with a passion for art, design, and technological progress. Their commitment to quality, sustainability, and innovation positions them as a reliable partner for businesses seeking to push creative boundaries and optimize production processes.
Cutting-Edge Equipment and Expertise
The company invests in state-of-the-art moulding machines capable of handling a wide array of materials, from thermoplastics to advanced composites. Their team of experienced engineers and designers collaborate closely with clients to develop bespoke moulds tailored to specific project needs, ensuring perfect fit, finish, and functionality.
Sustainable and Eco-Conscious Manufacturing
Recognizing environmental responsibilities, arti90.com emphasizes waste reduction through precise mould design, material recycling, and eco-friendly material options. This strategy not only enhances brand image but also resonates with the growing consumer demand for sustainable products.
Future Trends: The Evolving Role of Forming Mould in Business Growth
The evolution of forming mould technology is set to continue transforming industries with innovations like smart moulds integrated with IoT sensors for real-time quality monitoring, biodegradable mould materials, and AI-driven design optimization. These advancements will unlock unprecedented levels of efficiency, customization, and creativity for businesses leveraging arti90.com’s expertise.
Key Future Developments Include:
- Automation and Industry 4.0 Integration: Fully automated moulding lines with minimal human intervention
- Advanced Materials: Bioplastics, recycled composites, and innovative eco-friendly options
- Enhanced Design Tools: AI-enabled software for rapid mold design validation and optimization
- Sustainable Manufacturing: Circular economies through closed-loop moulding processes
Conclusion: Embracing Forming Mould for Competitive Advantage
In today’s creative and manufacturing landscapes, the forming mould stands as a cornerstone technology that empowers businesses to innovate, reduce costs, and accelerate time to market. Companies like arti90.com exemplify how leveraging advanced moulding techniques in art supplies, product design, and 3D printing leads to superior product quality, enhanced customer satisfaction, and sustainable growth.
Adopting forming mould strategies is no longer an option but a necessity for forward-thinking businesses aiming to dominate their sectors. The synergy between innovative design, technological mastery, and sustainable practices will define future success stories in the vibrant worlds of art, design, and manufacturing.